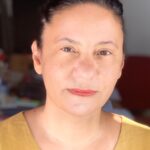
The invention refers to the development of a fractionation process for the recovery and valorization of the major components of brewers’ spent grain (BSG), which is the main byproduct in the beer production. The BSG production worldwide is ~40 million tons/year, ~8 million tons/year of which are produced in EU, and 240.000 tons/year in Italy. The reuse of BSG is attractive for brewing industry. In fact, the by-product selling markedly reduces the need for their disposal, while providing a source of income for companies.