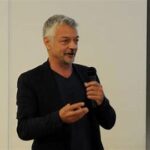
The invention concerns a wireless and passive transponder dedicated to vibration and pressure sensing, where the sensitive component only consists of transmission lines. In particular, the sensing element is a 3-dimentional directional coupler. This makes the sensor low-cost, lightweigth and suitable for green manufacturing technologies.
The transponder, connected to the device (“device under test” or DUT), is interrogated by a reader with a sinusoidal signal at frequency f0 (or carrier frequency). The DUT can be a vibrating platform, such as an aircraft or industrial machinery. If there are no vibrations, the transponder reflects the signal, without changing its spectrum. If the DUT is subjected to vibrations, however, the sensor uses the displacement caused by the vibrations to modulate the carrier frequency. In this way, the amplitude and frequency of the vibration are encoded in the sidebands of the reflected signal, and this information can be retrieved by the reader.