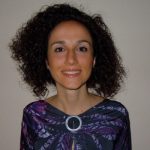
Martina Maselli
14:00 - 16:00
Artificial, bioartificial and tissue-engineered organs.
The device offered is a pneumatic braided muscle actuator, able to produce bidirectional force and motion, and variable stiffness. Pneumatic muscles are generally preferred thanks to their high power to weight ratio, light weight, easy to install, hazard-free use and inherent compliance. The existing/traditional pneumatic muscle actuator has a fixed braid fiber angle and is usually able to produce a pulling uni-directional force when actuated. Conversely this actuator is able to achieve variable stiffness depending on the braid angle.
Patent Status
DEPOSITATO
Priority Number
IT2015UB01717
Priority Date
26/06/2015
License
ITALY
Current Technology Limits
The invention is a compact pneumatic device that can be mass-produced with low costs using materials, machineries, and equipment commonly used in the industry. It follows the principles of the Mckibben artificial muscles type but conformed in such a way to overcome the known limits of realizations, in particular the possibility of being configured as desired in any time and with simple, effective and reliable constructive solutions.
Our Technology and Solution
Pneumatic artificial muscles usually consist of a hollow cylindrical elastomeric chamber covered by an outer braided sleeve, consisting of fibres made of un-stretchable material and arranged in an anti-symmetric helical configuration. The hollow internal chamber and the braided sleeve are tightly sealed and attached to rigid end fittings, a passage is provided through one of these end fittings for pressurizing the elastic chamber. The mechanical work done is transferred to an external system through these end fittings. The working principle of the Bi-directional actuator is based on the traditional pneumatic muscles but some fundamental changes enables the user to change the initial braid fiber angle independently. Depending on the braid angle, the actuator is able to produce extension and contraction upon pressurization, moreover the ability to change the initial braid fiber angle enables the actuator to achieve variable stiffness at each point along the total stroke of the actuator, whereas the traditional pneumatic muscles lack this ability.
Killer Application
The artificial pneumatic actuator can be applied in many aspects of rehabilitation robotics, from robotic prosthetics to rehabilitation devices. In addition, it can be used in industrial automation, for handling, locomotion, but also for automatic valve control. Thanks to its characteristics, the actuator is a simple and very light mechanical joint, where the muscle can also be used for controlling the rigidity of the rotating joint itself.
Advantages
The advantages of using this artificial pneumatic actuator are the high power/weight ratio, the force and the bi-directional motion and the possibility for obtaining maximum and variable rigidity at each point along the entire structure of the actuator. In addition, its use is compatible with human-machine interaction in terms of safety and it does not require a precise alignment during the installation phase thanks to its flexibility.
TRL
Il team