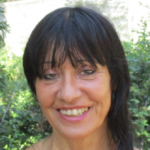
The invention refers to the development of a technology operating in continuous mode to produce organic polymeric membranes supported onto glass spheres of variable size, to obtain efficient, ready-to-use adsorbent systems, dimensionally stable over the time, based on a combination of low-cost, durable and operationally stable materials. It is a “all-in-one”, modular, controllable and safe process that can be automated, which enables the minimization of the materials losses as well as the exposition of the operators to reagents/solvents.
The adsorbent systems can be employed in numerous industrial sectors, particularly in water decontamination/potabilization processes.