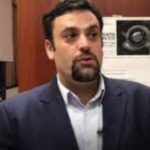
Innovative system in the aeration process and in the mix design of the components that make up Bio-Aerated Autoclavated Concrete (BAAC), a bio-cement for construction that is innovative in terms of energy saving and environmental sustainability. The innovation concerns the production process and consists mainly of the technology used to create the aerating agent, and in particular the use of micro-organisms (yeasts), which together with hydrogen peroxide generate the oxygen necessary for the formation of porosity and the reduction of the density of the block, obtaining values of mechanical resistance to compression and thermal conductivity that are fully in line with the values of similar commercial products.